I'm sure you know that aluminum is different from steel, since it's lighter, softer and more ductile. But did you know that there are actually three types of aluminum welders? The first is the most common type of welder who uses an E7018 electrode (like a mild steel welder). The second type uses an ER70S-10 (E7015) electrode at high amperages because it allows high currents without warping problems due to its more fluid core material. And the third type uses helium gas instead of argon because it's less expensive and easier to handle since helium doesn't have any odor or taste like argon does which makes it safer for welding indoors where sparks might ignite fumes from paint thinner or other flammable liquids.
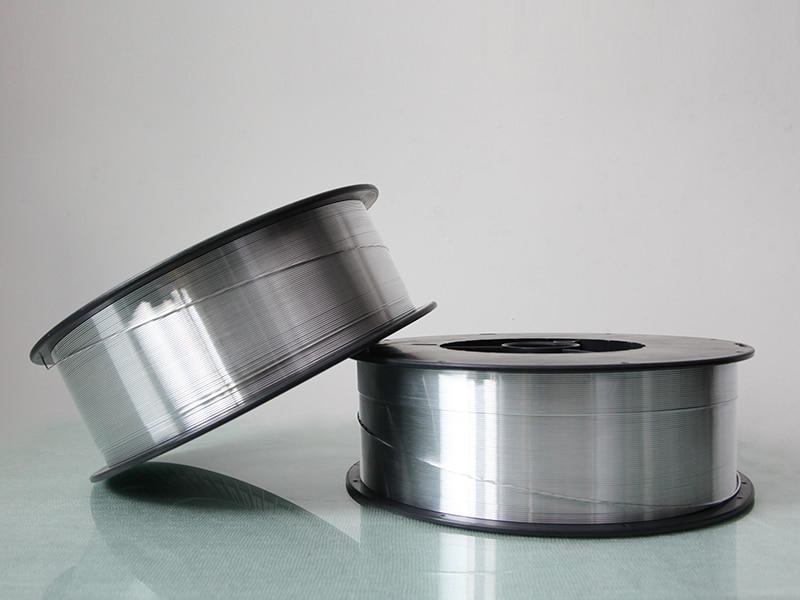
Aluminum is a great material for welding. It's easy to weld and requires less skill than other metals; however, it also has its own set of challenges in regard to welding techniques and materials selection. The most common type of aluminum wire used for MIG (Metal Inert Gas) or TIG (Tungsten Inert Gas) applications is called ER70S-6 which has a tensile strength of 70 ksi (483 MPa). This means that the material will break if stretched until it reaches a load equal to 473 times its own weight!
Aluminum is a good conductor of heat, which means it can transfer its energy easily. This helps aluminum welders to melt their material faster than other metals such as steel and stainless steel.
Another reason why we need aluminum welding wire is because aluminum has a lower melting point than both steel and stainless steel. The melting point of an element refers to the temperature at which it changes from solid form into liquid form (or vice versa). For example: Aluminum's melting point is 1,221 degrees Celsius (2,300 degrees Fahrenheit), while stainless steel's melting point lies between 1,473 - 2,650 degrees Fahrenheit depending on composition; therefore this makes it easier for us as we don't need any extra tools or equipment when working with them because they are already in liquid form so all you need do now is pour them onto whatever surface needs fixing or repairing!
Welding aluminum requires a different set of considerations from those of welding steel and stainless steel. The most important areas to consider are the types of joints you'll be making, the type of electrode you'll be using and the type of shielding gas necessary for your project.
The first thing to remember when welding aluminum is that it's not as strong as other metals. The second thing is that it tends to oxidize quickly when exposed to air or water--and that can lead to corrosion problems if not properly prepared beforehand (or cleaned up afterward). It's also important not to use too much heat because this can cause warping in your finished product; if this happens after soldering two pieces together then they won't fit together properly anymore!
The most important areas to consider are the types of joints you'll be making, the type of electrode you'll be using and the type of shielding gas necessary for your project.
When choosing a weld wire, keep in mind that it's not always necessary to use an aluminum alloy with a high melting point if you're just learning how to weld. In fact, using low-alloyed (easier) wires can actually help improve your technique because they melt at lower temperatures than higher-alloyed wires do, so they're easier to control when applying filler material during welding.
he type of joint you make depends on the thickness of your metal and how much heat it can withstand before becoming too soft or brittle. For example, if you're dabbing on small beads or fillets at relatively low amperage levels then an ER (E7018) or E6010 electrode will work fine with both argon or helium gas. If you're welding thicker material in a seam or joint with many layers then you want to use an E7018 electrode with helium gas. If you're welding something that's big like a trailer frame or large sign then an ER70S-10 (E7015) electrode is ideal since it allows higher currents without increasing warpage problems due to its more fluid core material.
The shielding gas used will depend upon what type of aluminum alloy you are working with, how thick the metal being welded is, and whether there are any other materials present in addition to pure aluminum such as silicon carbide particles which could cause flash burns when heated too rapidly during welding operations so require extra precautions during preheating stages prior to starting actual arc strikes against bare metal surfaces themselves.
We hope you've learned a lot about why we need aluminum welding wire. We also hope that this article has given you some ideas on how to use it in your own projects. Whether you're working with thin sheets or thick plates, there's an electrode for every job!