Aluminum alloy welding wire plays a crucial role in various industries due to its lightweight, high strength-to-weight ratio, and excellent corrosion resistance properties. The continuous development of welding wire technology has been instrumental in widening its application scope, leading to significant advancements and facing various challenges along the way.
Alloy Composition and Microstructure: Researchers have made significant progress in developing new aluminum alloys and optimizing their microstructures to enhance mechanical properties and weldability. Advancements in alloy composition have resulted in welding wires with improved strength, ductility, and weld performance, making them suitable for high-stress applications in aerospace, automotive, and construction industries.
Filler Wire Formulations: Continuous efforts in optimizing the formulation of welding wires have led to enhanced feedability, reduced porosity, and improved arc stability during welding processes. These improvements have resulted in higher welding efficiency, reduced defects, and improved overall productivity.
Surface Treatment and Coatings: Innovations in surface treatment techniques and coatings have addressed challenges like oxidation and hydrogen absorption during welding, leading to improved weld quality and reduced rework. Coated welding wires can ensure better arc initiation, reduced spatter, and increased resistance to environmental contaminants, positively impacting welding performance.
Automation and Robotics: The integration of automation and robotic welding systems has revolutionized the welding industry. The ability to control welding parameters with precision and consistency allows for efficient, high-quality aluminum alloy welding across different applications. Automated welding processes increase productivity, reduce labor costs, and ensure weld repeatability, especially in large-scale manufacturing.
Sensitivity to Contamination: Aluminum alloys are sensitive to contaminants like moisture, oil, and grease, which can lead to porosity and reduced weld integrity. Maintaining strict cleanliness and storage conditions for welding wires is crucial to ensure optimal performance and prevent defects.
Heat Affected Zone (HAZ) Cracking: Some aluminum alloys are prone to HAZ cracking during welding due to their thermal properties and susceptibility to solidification cracking. Welding techniques, filler wire selection, and preheating methods are essential considerations to mitigate this challenge and ensure sound weld joints.
Alloy Compatibility: Different aluminum alloys have varying compositions and melting points, making it essential to select the appropriate welding wire that matches the base metal. Mismatched alloys can result in reduced weld strength and integrity, limiting their use in critical applications.
Expensive Manufacturing Process: Producing high-quality aluminum alloy welding wire involves intricate processes and raw materials, contributing to its relatively higher cost compared to other welding wires. Manufacturers must balance the cost without compromising the wire's quality and performance.
In conclusion, the continuous advancements in aluminum alloy welding wire technology have expanded its applications in diverse industries, offering a lightweight and durable solution for various engineering challenges. While innovations have addressed many challenges, including weld quality and process efficiency, industry stakeholders must remain vigilant in addressing issues related to contamination, alloy compatibility, and weldability to further enhance the widespread adoption of aluminum alloy welding wire across different sectors.
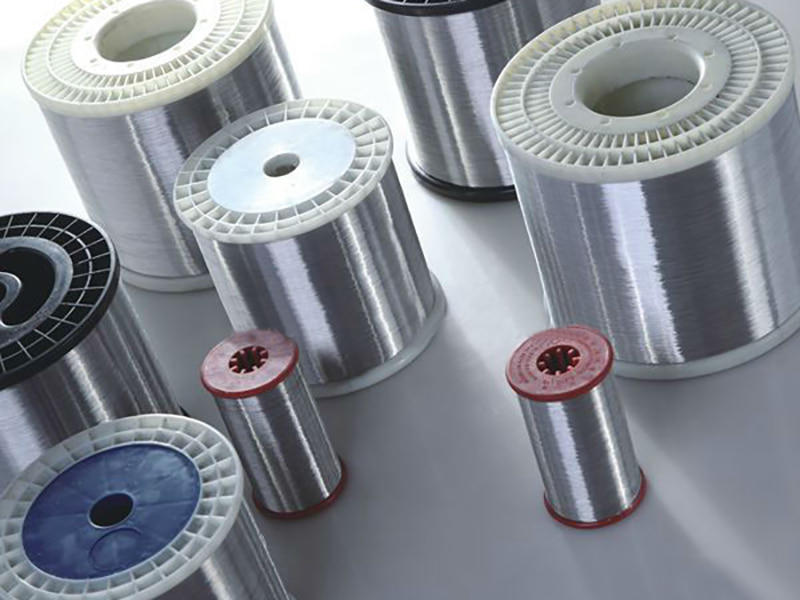