As we all know, the welding core is the metal core of the welding rod. In order to ensure the quality of the weld, there are strict regulations on the content of various metal elements in the welding core. In particular, there are strict restrictions on harmful impurities (such as sulfur, phosphorus, etc.), and the quality of the welding core metal should be better than that of the base metal. When purchasing, it is necessary to choose welding rods in a targeted manner, and conduct welding tests if necessary. For thick welded parts with complex structural shapes and high rigidity, due to the large internal stress during the welding process, the weld seam is easy to crack, so an alkaline low-hydrogen electrode with good crack resistance should be selected.
For weldments with small stress and difficult to clean the welding parts, acid welding rods that are not sensitive to rust, scale and oil should be selected. For weldments that cannot be turned over due to conditions, electrodes suitable for all-position welding should be selected. When the chemical composition of the base metal is high in harmful impurities such as carbon, sulfur, and phosphorus, electrodes with strong crack resistance and porosity should be selected, such as low-hydrogen electrodes. It needs to be clarified that the requirements for mechanical function and chemical composition of welded parts are not balanced. Some welded parts can pay attention to the requirements of strength and toughness. The strength between the base metal, or the high toughness of the weld metal; some welded parts can pay attention to the chemical composition requirements, such as the selection of heat-resistant steel, pay attention to the consistency of the chemical composition of the weld metal and the base metal; sometimes both Strict requirements, so when choosing welding rods, you should distinguish between primary and secondary, and consider comprehensively.
Aluminum Welding Wire can be welded with inert gas shielding (TIG, MIG welding). It can also be used for submerged arc welding. Stainless steel MIG welding can achieve high-quality welding automation and is easy to realize, and is widely used in surfacing welding, thin plate connection and other fields. The chemical composition of MIG welding wire is the same as that of welding wire TIG welding wire, but for some stainless steel varieties, there is another MIG welding wire with higher SI content, such as ER308Si, ER309Si, etc. corresponding to ER308 and ER309 welding wire, because the Si content is about 0.8% The surface tension of the droplet metal is reduced, the droplet particles become thinner, it is easier to achieve overspray, and the arc is more stable. At the same time, it can also increase the humidity of the molten metal, so that the weld bead has beautiful ripples, and it is not easy to cause lack of filling such as incomplete penetration, slag inclusions, and pores. Submerged arc welding uses stainless steel solid core welding wire, whose chemical composition is the same as that of gas shielded welding stainless steel welding wire, but it should use non-manganese-free low-silicon and high-fluorine melting flux.
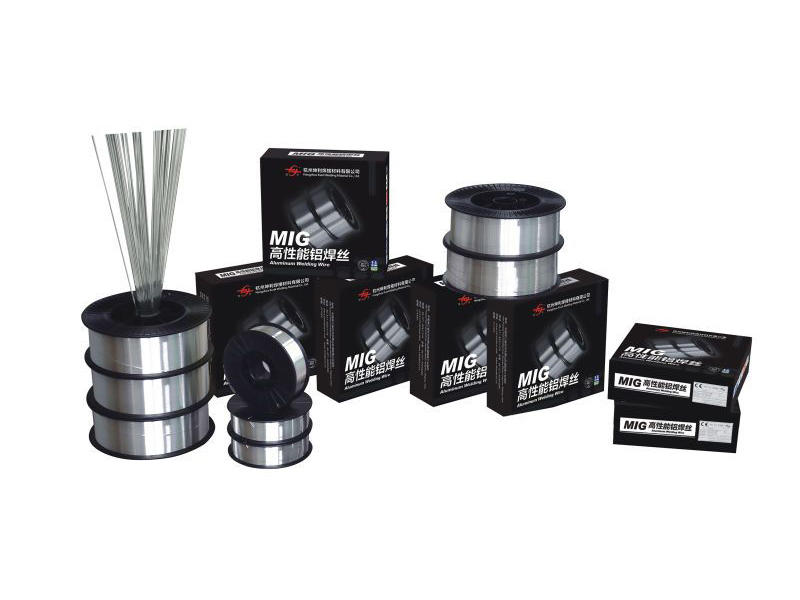
Stainless steel cored wire can be as simple as carbon steel and low alloy steel cored wire. The welding of stainless steel flux cored wire is mainly applied to MAG welding. MAG welding has the following characteristics; 1) Compared with manual welding, the deposition speed can be increased by 2 -4 times, the deposition efficiency is as high as 90% (only 55% for stainless steel electrodes) 2).
The current and voltage adaptability range is large, the welding conditions are easy to set, and the semi-automatic and automatic welding is easy. 3) Good slag removal and shiny weld bead surface. In addition, less spatter, good arc stability, X-ray qualified.